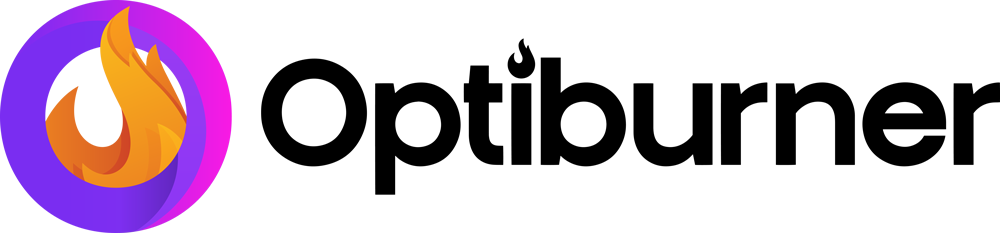
Optiburner © 2025 | Optiburner is a product of Funded Energy Solutions Ltd | Marketing & Web Design by Kris Studio
Discover how Optiburner's Dynamic Burner Management Unit (DBMU) enhances energy efficiency in manufacturing sites. Explore the benefits of this advanced boiler optimisation solution for lowering operational costs and reducing carbon emissions while maintaining production efficiency.
In the competitive world of manufacturing, every aspect of operational efficiency can affect a company's bottom line and market position. Among the many factors that contribute to operational costs, energy consumption—particularly in heating systems—often represents a significant and sometimes overlooked opportunity for improvement. As manufacturing processes demand consistent and usually high temperatures, the energy required for heating can constitute a substantial portion of a facility's overall energy usage.
Discover Optiburner's Dynamic Burner Management Unit (DBMU) - It's an innovative solution reshaping how manufacturing facilities approach energy efficiency in their heating systems. This cutting-edge technology provides a pathway to significant cost savings and reduced carbon emissions without compromising the crucial heating performance needed for manufacturing processes.
Manufacturing facilities face unique challenges regarding energy management, particularly in their heating systems. Unlike commercial buildings where heating might primarily be for comfort, heat is often an integral part of the production process in manufacturing. This creates a complex energy landscape with several key characteristics:
Many manufacturing processes require high temperatures maintained over long periods, resulting in substantial energy consumption.
Fluctuations in temperature can affect product quality, making consistent heat delivery essential.
Different manufacturing facility areas may have vastly different heating requirements, from climate control in office spaces to high-temperature process heating on the factory floor.
Many manufacturing facilities operate around the clock, meaning heating systems must perform consistently at all hours.
In an industry where margins can be tight, the cost of energy for heating can significantly impact overall profitability.
With increasing focus on sustainability and environmental regulations, manufacturers are under pressure to reduce their carbon footprint.
Traditional heating systems often struggle to meet diverse and demanding requirements efficiently. This usually leads to excessive energy consumption, unnecessarily high operational costs, and a larger-than-necessary carbon footprint. Therefore, there is a clear need for a more intelligent and adaptive solution that can optimise heating efficiency without compromising the critical role of heat in manufacturing processes.
The Optiburner Dynamic Burner Management Unit (DBMU) is a sophisticated device designed specifically for industrial boilers. It is ideally suited for the complex heating needs of manufacturing facilities. Unlike conventional heating control systems, which focus on managing space temperatures, the DBMU takes a more fundamental approach by optimising the boiler's firing pattern.
At its core, the DBMU is an intelligent control system installed between the boiler's thermostat and burner valve. This strategic positioning allows it to intervene in the boiler's operation without disrupting existing temperature control systems within the facility. The primary function of the DBMU is to alter the boiler's firing pattern, creating fewer but slightly more extended burn periods. This subtle yet powerful adjustment leads to substantial energy savings over time without affecting heat delivery to the facility.
The science behind the DBMU's operation is rooted in Isaac Newton's Law of Cooling, a principle that describes how a body's rate of heat loss is directly proportional to the difference in temperature between the body and its surroundings. By leveraging this principle, the DBMU extends the boiler's cooling cycle by approximately 90%. This extension allows the boiler temperature to drop by around 3 degrees Celsius before refiring, resulting in more efficient energy use.
In manufacturing facilities, where heating demands are often high and critical to operations, the DBMU offers a unique approach to energy efficiency that doesn't compromise performance. Here's a deeper look at how it functions in this specific context:
The DBMU is designed for easy integration into existing heating systems. It's installed between the thermostat and the burner valve, requiring no modifications to the central boiler or heating infrastructure. This means it can be implemented with minimal disruption to manufacturing operations - a crucial factor in an industry where downtime can be extremely costly.
Once operational, the DBMU begins analysing and optimising the boiler's firing pattern. Creating fewer but slightly more extended burn periods reduces the boiler's overall time burning fuel. In a typical scenario without the DBMU, a boiler might cycle through 8 burns of 10 minutes each in 4 hours. With the DBMU in place, this could be reduced to 5 burns of 12.5 minutes each. This adjustment results in a significant reduction in total burn time and, consequently, in fuel consumption.
The DBMU's operation leverages Isaac Newton's Law of Cooling to achieve greater efficiency. By extending the boiler's cooling cycle, the DBMU allows the boiler to cool slightly more between firing cycles. When the boiler does fire up again, it runs for a slightly more extended period, but the overall effect is a reduction in total burning time and fuel consumption. This scientific approach ensures that energy savings are achieved without compromising the boiler's ability to meet heating demands.
One of the most crucial aspects of the DBMU's operation in manufacturing settings is that despite these adjustments to the boiler's firing pattern, there's no variation in heat output. This ensures that the temperatures critical for manufacturing processes are maintained consistently. Production lines, material processing, and other heat-dependent operations receive the same stable temperatures they require, but the energy used to maintain these temperatures is significantly reduced.
Manufacturing facilities often have varying heating needs depending on production schedules, shifts, and seasonal changes. The DBMU is designed to adapt to these changing demands automatically. Whether it's a peak production period requiring maximum heat output or a quieter period with reduced heating needs, the DBMU continually optimises the boiler's operation to match the current requirements.
The DBMU comes with a built-in protocol for identifying and verifying the savings being made. It runs for 50 cycles, measuring each cycle's cooling and burning phase and taking the average. This data allows facility managers to see concrete evidence of the energy savings achieved, which can be crucial for justifying the investment and ongoing energy management strategies.
The implementation of Optiburner's DBMU in manufacturing facilities leads to a range of significant benefits:
Manufacturing facilities using the Optiburner DBMU typically see more than 16% fuel consumption reductions, with savings often reaching 20% to 25%. Large industrial operations with substantial heating requirements can translate to enormous cost reductions. Consider a manufacturing plant that spends £1 million annually on heating fuel. A 20% reduction would result in savings of £200,000 per year - a significant amount that could be reinvested in the business or contribute directly to increased profitability.
In capital-intensive manufacturing, any significant investment must demonstrate a quick return. The DBMU delivers on this front, with payback periods ranging from 5 to 18 months, depending on consumption. This rapid ROI makes the DBMU an attractive option even for facilities operating under tight financial constraints. The quicker the payback, the sooner the manufacturing facility can start reallocating the saved funds to other critical areas of operation or seeing direct improvements in profit margins.
As the manufacturing sector faces increasing pressure to reduce its environmental impact, the DBMU offers a powerful tool for significantly reducing carbon emissions. Reducing fuel consumption directly translates to a decrease in CO2 emissions. For a typical manufacturing facility, this could mean hundreds or even thousands of tonnes of CO2 emissions avoided each year. This aligns perfectly with corporate sustainability goals and can help facilities meet increasingly stringent environmental regulations and targets.
Any upgrade or installation that disrupts normal operations in a manufacturing setting can have serious financial consequences. The DBMU's design considers this, allowing for installation with minimal disruption to production schedules. The unit can typically be installed in a matter of hours, often without any need to shut down the heating system entirely. This means that production can continue uninterrupted while the facility takes a significant step towards greater energy efficiency.
With over 10,000 successful installations and no reported issues, the DBMU offers the reliability and consistency that manufacturing facilities demand. In an environment where equipment failure can lead to costly downtime, this track record of reliability is crucial. Knowing that they're implementing a tried and tested solution provides peace of mind for facility managers and executives.
As the only boiler optimiser certified by the Building Research Establishment (BRE), the DBMU provides manufacturing facilities with a trusted, independently verified solution. This certification is a testament to the DBMU's effectiveness and can be valuable when justifying the investment to boards or funding bodies. It also aligns with the manufacturing sector's emphasis on quality and certified processes, extending this principle from production to facility management.
The benefits of implementing the Optiburner DBMU extend beyond immediate energy and cost savings, having a broader impact on overall manufacturing operations:
Every cost reduction can make a difference in an increasingly competitive global market. The significant energy savings the DBMU provides can allow manufacturers to price their products more competitively or invest in other business areas to gain a market edge.
With consumers and B2B customers increasingly valuing sustainability, the reduced carbon footprint achieved through the DBMU can enhance a manufacturer's green credentials. This can be a valuable marketing point and may open new market opportunities with environmentally conscious clients.
As energy efficiency regulations become more stringent, particularly for industrial operations, the DBMU helps manufacturing facilities meet compliance requirements. By proactively implementing solutions like the DBMU, manufacturers can ensure they're meeting current standards and well-prepared for future regulatory changes.
By reducing overall energy consumption, the DBMU can enhance energy security for manufacturing facilities. In the event of energy supply disruptions or price spikes, facilities with lower baseline energy needs are better positioned to maintain critical operations. This increased resilience can be crucial in ensuring continuity of production during challenging times.
The detailed performance data provided by the DBMU allows for more informed decision-making about energy use and system performance. This aligns with the broader trend towards data-driven manufacturing and can contribute to overall operational optimisation.
Recognising the unique needs and challenges of the manufacturing sector, Optiburner offers a comprehensive service for industrial facilities implementing the DBMU:
Optiburner's team of experts thoroughly assesses the facility's current heating system and energy use patterns. This allows for a customised proposal that outlines projected savings and the optimal implementation strategy, considering the specific manufacturing processes and heating requirements.
Qualified technicians who understand the specific requirements of industrial environments carry out the installation process. They work to ensure minimal disruption to production schedules, often completing the installation during planned maintenance periods or off-peak hours.
Post-installation, Optiburner provides ongoing support to ensure the DBMU continues to operate at peak efficiency. This includes regular check-ups and any necessary adjustments or updates to the system to ensure it continues to meet the changing needs of the manufacturing facility.
Optiburner provides regular efficiency reports to help manufacturing facilities track their savings and optimise their energy use further. These detailed reports offer insights into energy consumption patterns, savings achieved, and potential areas for further improvement.
Training for Facility Staff: Optiburner offers training sessions for facility management staff to ensure that in-house teams can make the most of the DBMU. This empowers the manufacturing facility to manage its energy use more effectively in the long term and integrate the DBMU's operation with other energy management initiatives.
In an era where manufacturing facilities are under increasing pressure to optimise resources, reduce costs, and minimise their environmental impact, Optiburner's Dynamic Burner Management Unit offers a powerful solution. By significantly reducing energy consumption and carbon emissions without compromising performance or production requirements, the DBMU is helping manufacturing companies across various industries achieve their efficiency and sustainability goals.
The DBMU's ability to deliver substantial cost savings without disrupting operations, its rapid return on investment, and its contribution to reducing carbon emissions make it an ideal fit for the unique needs of manufacturing facilities. Its proven track record of reliability and BRE certification ensure that industrial operators need when implementing new technologies.
As the manufacturing sector continues to evolve, facing challenges from global competition, rising energy costs, stricter environmental regulations, and increasing demand for sustainable practices, innovative solutions like the Optiburner DBMU will play a crucial role. They will help create more efficient, sustainable, and cost-effective manufacturing facilities that are better equipped to meet the production demands of the future while maintaining a competitive edge in the market.
For manufacturing executives and facility managers looking to significantly reduce their energy bills and carbon footprint, the DBMU represents a smart, proven investment in the future of their operations. It's not just about saving energy; it's about creating more efficient, sustainable, and competitive manufacturing processes that can thrive in an increasingly challenging business environment.
Is your manufacturing facility ready to take a significant step towards energy efficiency and improved resource allocation? Contact us today for a personalised consultation. Our team of experts will assess your facility's unique needs and demonstrate how the Dynamic Burner Management Unit can transform your heating system's efficiency. Take the first step towards substantial energy savings and a reduced carbon footprint with Optiburner.
Contact us for a no-obligation consultation. Our energy efficiency specialist will explain how the Optiburner DBMU works and create a customised burner management plan for your business. This plan ensures your ROI, maximises energy savings, and minimises carbon emissions. We also offer complete maintenance of the Boiler Optimisers as part of the package for complete peace of mind.
During the site visit, our BRE-certified engineers will comprehensively assess the compatibility of your boiler and heating systems. This thorough process is crucial to designing the optimal boiler optimisation setup, maximising energy savings, reducing fuel consumption, and guaranteeing payback within two years. We will then schedule an installation date that works best for your business.
Our BRE-certified engineers will install the Optiburner units in your boiler room and ensure everything complies with current health and safety regulations. The DBMU software will be updated and fine-tuned for your boiler type to ensure maximum performance and energy savings. The installation process is quick, minimally disruptive, and guarantees the safety and efficiency of your operations.
After installation and testing, our engineers will recommend supply and fit options, including retrofit installation and valve insulation. You will receive quick training on operating the Optiburner units and using the remote download feature to monitor and report energy savings easily. Expect to save 15% or more on energy bills over a year, with results in the downloadable Savings Report directly from the DBMU unit.